10 Uses for a Raspberry Pi in Manufacturing
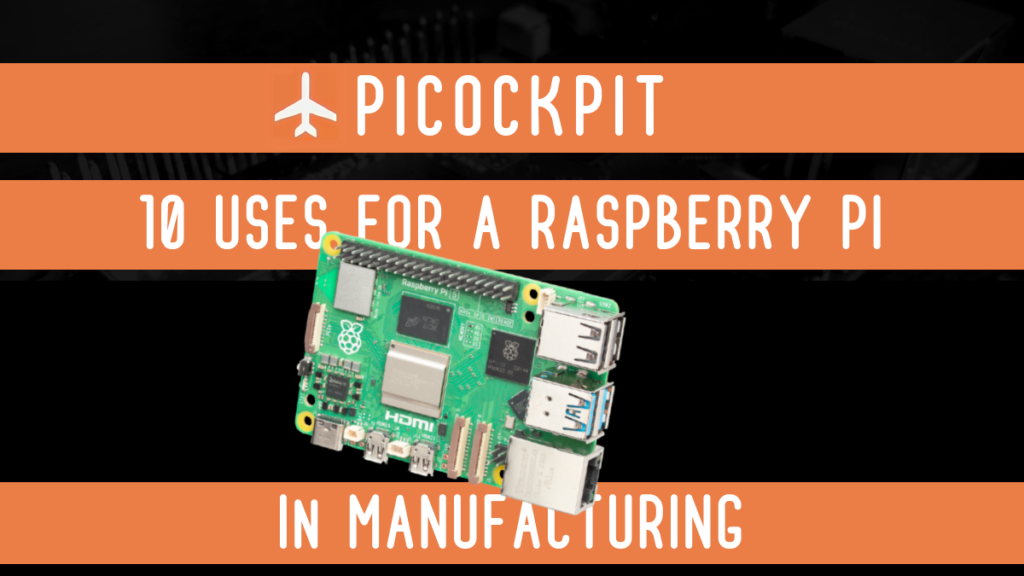
The advent of affordable and versatile single-board computers, such as the Raspberry Pi, has sparked a revolution in various industries. This revolution is perhaps most obvious in manufacturing itself.
These compact devices, initially designed for educational purposes, have found a multitude of applications on the factory floor. Indeed, even Raspberry Pi nodes are used in the production process, as Jeff Geerling demonstrated in this video:
So in this blog post, I’ll explore the top 10 uses for Raspberry Pi in manufacturing, showcasing how these small but powerful devices are transforming the way companies approach their production processes.
The Top 10 Uses
1. Industrial IoT Gateways:
Raspberry Pi nodes serve as an excellent Industrial Internet of Things (IIoT) gateway, connecting manufacturing equipment to the internet for real-time monitoring and data analysis.
Since a Raspberry Pi is both small and durable, they offer the best options for many IIoT solutions. And by bring IIoT into manufacturing, companies can improve their decision-making, predictive maintenance, and overall process optimization.
2. Quality Control Systems:
Implementing image recognition and machine learning algorithms on Raspberry Pi allows for the development of cost-effective quality control systems. A few months ago, I wrote about the Google Coral USB Accelerator, which you can pair with a Raspberry Pi for exactly these purposes.
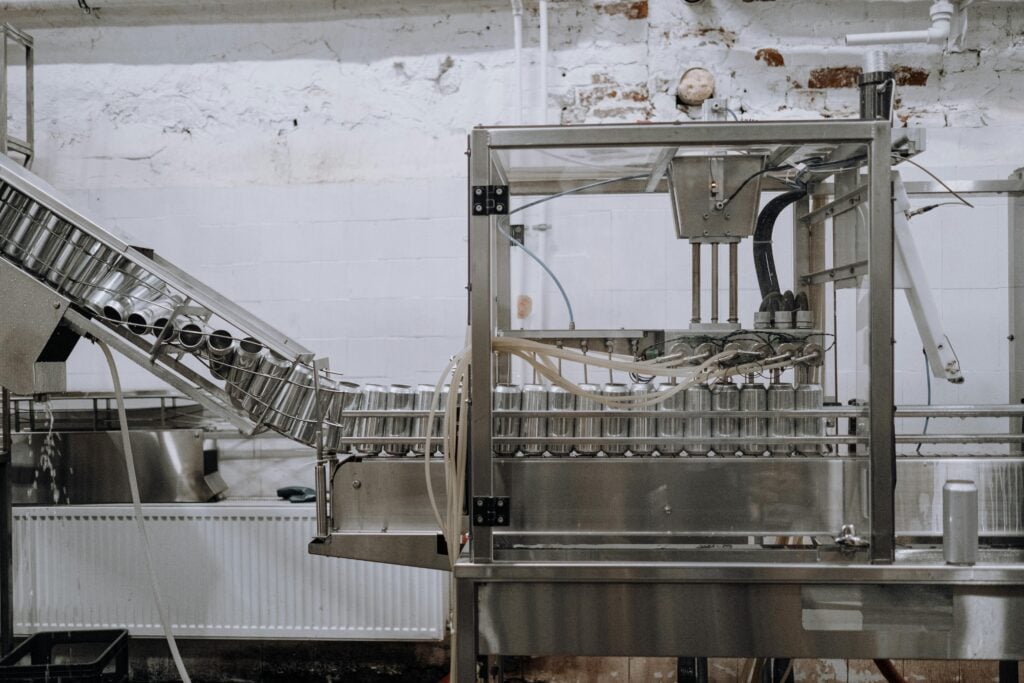
These systems can identify defects, ensuring that only products meeting specified standards move down the production line, which you can see in the Jeff Geerling video above.
3. Inventory Management:
Raspberry Pi can be integrated into inventory management systems to monitor stock levels, track assets, and automate reorder processes. If you want to find ways of developing a customized inventory management system, you can develop scripts that you could then run with our PiControl App through PiCockpit.
This leads to more efficient supply chain management and reduces the risk of stockouts or overstock situations.
4. Automated Testing Stations:
Building automated testing stations with Raspberry Pi facilitates the quick and accurate assessment of manufactured components. These sorts of testing stations also appear in the Jeff Geerling video above.
This ensures that products meet predefined criteria before advancing further in the production process, enhancing overall product quality.
5. Energy Monitoring and Management:
You can also use a Raspberry Pi to create energy monitoring systems that track power consumption across different manufacturing processes.
This data enables businesses to identify energy inefficiencies, optimize usage, and implement sustainable practices. You can also explore potential carbon-zero options for your manufacturing process.
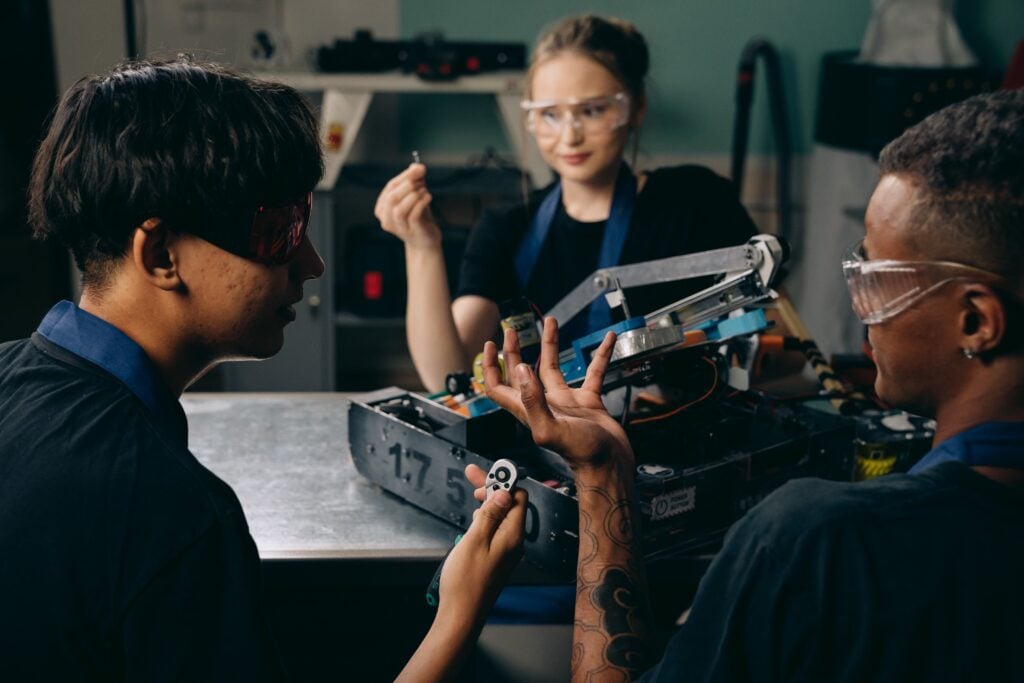
If you’re curious about the energy costs of a Raspberry Pi itself, you can check out our Pi Power Cost Calculator. It’s a free and quick tool to calculate your energy expenses with a Raspberry Pi.
6. Worker Safety Systems:
A company can enhance worker safety with Raspberry Pi by developing systems that monitor environmental conditions, such as temperature, humidity, and air quality.
Here, another PiCockpit App can come in handy. Our BME688 AirMeter App measures temperature, humidity, air pressure, and indoor air quality.
7. Production Line Automation:
A few months ago, SB Components Ltd started a Kickstarter for PiArm – a Raspberry Pi-powered robotic arm. Indeed, you can employ a Raspberry Pi to automate all sorts of tasks within the production line, including controlling robotic arms, conveyor belts, and other machinery.
This leads to increased efficiency, reduced labor costs, and minimized errors in repetitive tasks.
8. Remote Equipment Monitoring:
Remote equipment monitoring is one of the most obvious benefits of bringing a Raspberry Pi into manufacturing, in my opinion.
This allows engineers and managers to keep an eye on machine health, receive alerts for potential issues, and perform troubleshooting without being physically present on the factory floor.
You could also use a Raspberry Pi camera in order to keep an eye on the equipment over stream.
9. Training Simulators:
Raspberry Pi can power training simulators for manufacturing processes. Training simulators are an important part of giving new employees a risk-free environment where they can learn how to do their job well.
These simulators provide a cost-effective and safe environment for training new employees, reducing the learning curve and minimizing the risk of errors on the actual production floor.
If your company wants a virtual environment to train people you could use a Raspberry Pi as a far cheaper alternative to run the virtual plant.
And, finally, the last top use for a Raspberry Pi in manufacturing is:
10. Customized Human-Machine Interfaces (HMIs):
A Human-Machine Interface is a simply a control panel or display that allows people to easily manage and monitor machines.
Many companies these days are developing custom HMIs using Raspberry Pi to provide intuitive control interfaces for operators on the factory floor. This makes it both easier and far more efficient for operators to keep track of what different machines are doing.
Most importantly, it prevents human error in tracking everything.
Finally, HMIs enable easy interaction with complex machinery, contributing to increased productivity and reduced training time.
Conclusion
The versatility and affordability of Raspberry Pi have made it a game-changer in the manufacturing industry, of course.
If you’re using Raspberry Pi nodes in manufacturing, then check out PiCockpit and see how we can improve your production.
You can sign up with one click and it’s free for up to 5 Raspberry Pi nodes:
From streamlining production processes to improving worker safety and enabling real-time data analytics, the applications of Raspberry Pi in manufacturing are diverse and impactful.